This article by Tim Page-Bottorff was originally published in the
February 23, 2015 issue of Safety+Health Magazine
Once you’ve finished an incident investigation, how do you use investigation data to prevent similar incidents from occurring again?
QUESTION: Once you’ve finished an incident investigation, how do you use investigation data to prevent similar incidents from occurring again? Responding is Tim Page-Bottorff, CSP, senior safety consultant at SafeStart, Belleville, Ontario.
By their very nature, incident investigations are reactionary. But properly collecting and studying investigation data, and then clearly communicating the findings, will provide the best opportunity to prevent similar incidents in the future.
A decision is only as strong as the data it’s based on, and an investigator must properly collect data about the incident under investigation. In most cases it will make sense to use a fault tree analysis, root cause analysis or what-if checklist. These tools can be obtained from OSHA or by following the OSHA Process Safety Management Standard (29 CFR 1910.119). Adhering to the OSHA hierarchy of controls is the preferred model to identify the root cause of an incident. During the data collection phase, you can also identify any significant human factors and potential cultural issues within the organization/department.
Most safety professionals are already familiar with the tools mentioned above. However, this knowledge can lead many to approach the investigation with a preconceived solution in mind, which can derail an investigation before it has begun. Keep in mind that performing an investigation will help you determine what caused a single incident, and an analysis of larger behavioral trends is the first step in preventing a range of similar issues going forward.
To avoid future incidents you need to put the data you’ve collected to good use by thoroughly and impartially analyzing it. Examine the metrics to see if the incident is part of a larger pattern. At a minimum, you should be looking at data that covers several years of organizational and departmental safety performance. If you are trending in certain areas you can make adjustments to your safety management system.
There are two main types of trends you will notice. A series of incidents that are all functionally identical may point to a problem with the hierarchy of controls, and an engineering solution may be a suitable course of action.
However, engineering solutions are often unable to completely address issues such as slips, trips and falls – or workers making poor decisions, taking safety shortcuts or forgetting to wear their personal protective equipment. A broader pattern of incidents may indicate that your company will be best served by implementing a long-term solution to address human factors in addition to ensuring the hierarchy of controls is sufficiently robust.
Don’t underestimate the value of properly communicating the results of an investigation. You should deliver a detailed report to management and also post a summary of your findings for employees. If you are implementing an engineering solution, then outline any changes that will be made to help prevent that incident from happening again.
If human factors played a role in the incident, then communicating corrective measures to employees may be more challenging because nobody is intentionally trying to get hurt. Simply telling them to stop unsafe behavior will only provide a temporary fix at best; you will most likely be better served by integrating regular human factors training alongside the existing hierarchy of controls.
Although both are necessary and important, the big difference between engineering and human factors solutions is that engineering improvements typically only prevent the exact same incident from occurring again (installing a guardrail at that location) whereas addressing the human factors (keeping eyes and mind on task or looking before moving) will prevent similar incidents from occurring throughout the plant or even off the job. An impartial assessment of your safety data will guide you in determining which type of solution will provide the biggest benefit.
Tim Page-Bottorff, CSP, CET is a senior SafeStart consultant, past president of the ASSP Arizona Chapter and a former United States Marine. As an OSHA trainer he is well-versed in how to facilitate effective training sessions and he frequently speaks about training and other safety topics at national safety conferences.
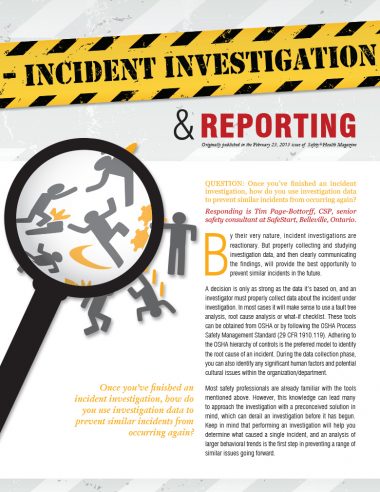
Get the PDF version
You can download a printable PDF of the article using the button below.