Background
You don’t stay in business for nearly eight decades unless you’re doing a lot of things right. Through a depression, a world war, numerous recessions and an era of dramatic technological innovation, Quincy Compressor has earned loyal customers worldwide, some of who proudly point to the company’s air compressors and vacuum products that have been on-the-job for decades.
Commitment to quality continues to be a cornerstone to Quincy Compressor’s success. However, it’s the company’s commitment to safety that has drawn recent accolades. The company boasts a safety program so successful that Occupational Hazards magazine recognized Quincy Compressor as one of America’s safest companies.
The company’s dedication to safety, from the plant floor to the front office, is at the heart of the program’s success, explained Sharon Oenning, Quincy Compressor’s Human Resources Manager: “We think of every one of our 140 employees as a safety engineer.” Oenning, who directs the safety program at the company’s plant in Bay Minette, Alabama, explained that SafeStart has played an integral role in the program’s success.
Occupational Hazards magazine recognized Quincy Compressor as one of America’s safest companies
Training need
Quincy Compressor was making good progress with their safety program, reducing recordable accidents by 48% in three years. The company performed safety audits, carefully analyzed the cause of accidents and provided basic safety training to employees. Yet the company’s safety engineer knew there was always room for improvement. How could Quincy Compressor encourage employees to not only participate in a safety program, but to take ownership of and responsibility for ensuring a safe workplace? In researching behavior-based safety as a potential solution, Quincy Compressor’s safety engineer came across a brand-new safety-awareness training program called SafeStart.
“We liked SafeStart immediately and decided to implement it,” said Oenning. “It’s simple, easy to understand and just plain common sense. Our employees can relate to it and use it at work and at home.”
In researching behavior-based safety as a potential solution, Quincy Compressor’s safety engineer came across a brand-new safety-awareness training program called SafeStart
Implementation
Quincy Compressor rolled out its first SafeStart class in the later part of year 1, training all employees on how to recognize the situations and states that could lead to unsafe behaviors. The program’s five modules use scenariobased videotapes and workbook exercises reinforced by facilitator-led discussion to help participants keep hazards in mind and in sight on-the-job, off-the-job and on-the-road. Every Quincy Compressor employee takes a SafeStart refresher course once a year in January.
While SafeStart plays a key role, it is just one of many elements of Quincy Compressor’s comprehensive safety program, Oenning explained. The SafeStart philosophy and language, however, impacts and complements several of Quincy Compressor’s other safety initiatives.
The company empowers employees— salaried and hourly workers alike—to identify and remedy unsafe situations through monthly safety audits and reporting of near-miss incidents. SafeStart equips employees with a common framework and language to analyze and describe habitual or unintentional behaviors as they conduct audits or document near-miss incidents. Nearmiss incidents are reported and posted in safety bulletins as they occur for reinforcement, added Oenning, and are often described using SafeStart terms like ‘eyes on task’ or ‘line-of-fire.’
While SafeStart plays a key role, it is just one of many elements of Quincy Compressor’s comprehensive safety program
Results
In the five years since Quincy Compressor first implemented SafeStart, the company dramatically improved its already-strong safety record. Not a single employee has missed work due to injury. The company’s twelve recordable incidents in year 1 declined to five in year 2, three in year 3, two in year 4 and none in Year 5. In fact, as of the summer of year 6, Quincy Compressor had gone twenty-one months without an accident.
One of the key business benefits, said Oenning, is reflected in the company’s workers’ compensation costs for year 5, which came to a grand total of fiftyfive dollars.
Quincy Compressor’s former parent company, Enpro Industries noted another important windfall when it highlighted the Bay Minette plant’s success story in the corporation’s annual report: the plant is not only one of the organization’s safest facilities, but also among the most efficient, boasting an on-time delivery rate of 96%. “Safe workers,” the report observed, “are productive workers.”
Not a single employee has missed work due to injury
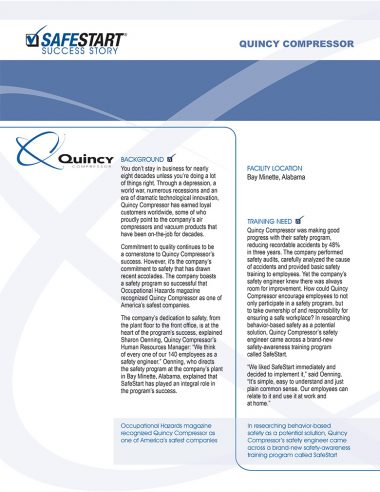
Get the PDF
You can view or download a PDF of this case study using the button below.