How Mineração Taboca Reached 2 Million Collective Hours Without Accidents
Safety beyond traditional rules and procedures
Mineração Taboca was founded in 1969, and it is one of the few companies active in the world tin market to have its own mine (Pitinga), located in the Amazon Region, in the municipality of Presidente Figueiredo, Brazil. The company operates in the research, mining, and marketing of tin, niobium, and tantalum.
In addition to the Amazonas unit, Mineração Taboca also has a metallurgical unit in Pirapora do Bom Jesus, São Paulo, Brazil, where it produces 99.9% pure refined tin.
The company is part of the Mining Division of the Peruvian business group Breca, which has more than 130 years of history enhancing progress, protecting the environment, and building the future.
Units
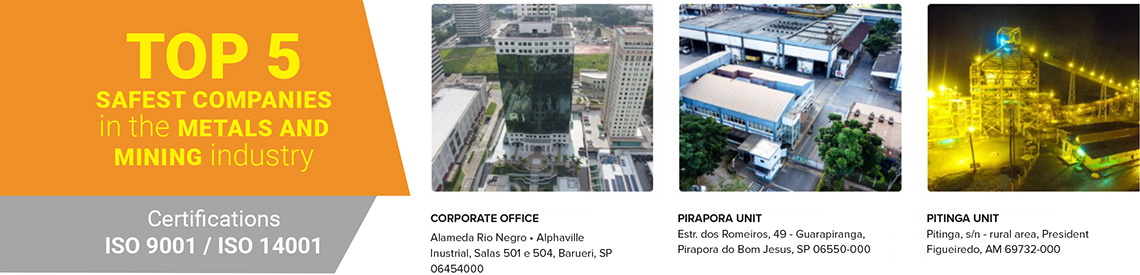
Challenge
In the words of Taboca’s Director of Operations, Eduardo Orban, the company’s main challenge was to take occupational safety to another level. A project was initiated to improve the physical conditions of the sites and invest in training for employees with the sole objective of reducing work accidents.
But people kept making mistakes, even a few days after implementing several initiatives aimed at reducing accidents.
Going beyond the traditional methods
The company realized that it should implement a different strategy from the traditional ones already practiced. The managers noticed that most of the accidents were linked to human factors. “We need to understand how people work, and with that, we will be able to change the focus on safety that was being implemented,” said Orban.
SafeStart came at the right time, and Taboca realized that it was the most assertive program to address exactly what they needed to understand better: human factors.
We still have a long way to go, a lot to overcome, but there is no question that the change in company culture with regard to the health and safety of our team led us to a level that I never imagined we would reach.
– Eduardo Orban
Director of Operations at Mineração Taboca.
Culture change and benchmark in mining
The implementation of SafeStart in the Pirapora unit was part of a set of other parallel actions that were already happening in the company. Shortly after SafeStart was implemented, there was a positive change in how the employees viewed safety and a noticeable change in their risk perception.
As a result of these changes, according to Minsur S.A. Corporate Health and Safety Manager Belisario Perez the Pirapora unit achieved significant recognition and became the benchmark for occupational safety in Latin America’s mining industry.
In September of the same year, they celebrated three years without accidents with reportable injuries (without leave):
“We have become a reference because we are changing the culture of people to worry about their safety and that of others, before they worry about production,” said Eduardo Orban.
And he adds: “There is still a long way to go, a lot to overcome, but there is no question that the change in company culture with regard to the health and safety of our team has led us to a level that I never imagined we would reach.”
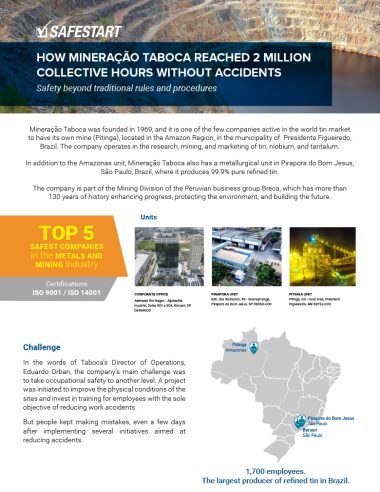
Get the PDF
You can view or download a PDF of this case study using the button below.