In nature, fish school together for safety and efficiency—it allows them to conserve energy, have greater success with foraging and their social functions are better supported, increasing communication and reducing stress. The folks at High Liner Foods know fish better than anyone and they also know that those exact principles of schooling fish apply to business.
Having operated for over one hundred years, High Liner has safety reeled in. They have a strong set of policies and procedures that enable employees to conduct their work safely. They know that safety is reliant on the same symmetry, coordination and dependence on one another that a school of fish executes, so their holistic approach stretches beyond compliance and weaves safety throughout the company, infl uencing its culture and making safety an everyday function.
Like a school of fish acting on one impulse, a culture drives people to collectively act under the same set of beliefs and impacts their daily activities. This is why High Liner promotes company-wide accountability and provides strong support for the EHS programs, changing collective beliefs and impacting behaviors.
Employee Involvement
Employee involvement is so important at High Liner that they’ve made it part of their mission: Our secret to success is simple. It’s our people. In fact, the company believes in building a high-performance organization by investing in their people—as High Liner Foods U.S. Operations Technical Trainer Lauren Lamontagne boasts,
We take immense pride in our training program, which provides employees not only with the tools to do their job safely and successfully but also with the awareness and skills to live and breathe safety in their everyday lives.
But anyone with a good safety program knows that there’s always room for improvement. Each year, the High Liner EHS department develops a training plan for the coming year looking at current performance vs. targets to ensure the future programs address the gaps identified through this analysis. In the past, this approach uncovered a need to implement a program that focused on human factors. It had to work in conjunction with their existing safety program and meet three key areas of safety: on-the-job safety, off-the-job safety and driving safety. High Liner also wanted to make zero accidents a reality and knew that they needed something more than a standard safety program to achieve that.
SafeStart
In 2013, a new administration with prior behavior-based safety experience pushed for changes to close the gaps they identified in the existing safety program. With SafeStart they found a keeper; it was the only program among the ones considered that addressed the three key areas of safety they were looking for—especially 24/7 safety—with proven results for accident reduction.
On-the-job Safety
For High Liner Foods, safety takes precedence from the moment an employee is hired. All employees receive an introduction to the SafeStart program on day one. By immediately immersing these new employees in the SafeStart culture, they are infl uenced from the start by management and their peers in terms of expectations and self-accountability when it comes to safety. SafeStart provides a common safety language, which is great in a workplace that trains in six different languages to accommodate the variety of cultures among employees. By recognizing and adapting to the needs of a multicultural workforce, any company can develop a greater emotional connection between the workers and the organization. The result will be a fully realized safety culture with employees that are more likely to take personal responsibility for their safety and more motivated in their duties.
Regardless of the situation or setting, people are creatures of habit. Wherever they are, when something outside of the norm arises and they don’t know what to do, they will look to someone in authority to show them the way. The High Liner management team’s commitment to SafeStart has been unwavering and it’s a big part of their success with the program.
“Upper management was involved in the process from day one, including attending the SafeStart consultations on-site,” said Lamontagne. “I think this really helped to drive home the impact that SafeStart can have on safety performance, so long as it’s given its due attention and planning.” Just as importantly, front-line supervisors and safety leaders are great SafeStart champions who, through their dedication and infl uence, help ensure that the employees at High Liner have the awareness and skills to do their job safely and carry that through into their everyday lives.
Zero Accidents is Possible
SafeStart has gone far beyond infl uencing the safety culture at High Liner and the results can be clearly seen in their accident rates. High Liner’s company-wide OSHA Incident Rate prior to SafeStart was 4.3. After SafeStart this number fell to 1.3 with almost 90% training completion among employees (the rate is under 0.1 among SafeStart grads). That’s a 70% reduction in recordables after two years of practicing SafeStart.
High Liner immediately noticed that their downtime related to incidents, as well as the number of incidents themselves, decreased. They also noticed a significant downturn in recurring injuries and the actual incidents seem much less severe and rarely result in lost time. Consequently, significantly less retraining is required.
Off-the-job Safety
High Liner also recognized that safety training must continue outside the workplace. After all, off-the-job injury rates are more costly in many ways—from reduced productivity and absenteeism to high replacement and retraining expenses.
The SafeStart home program is a key factor in creating a positive shift in safety culture through improved safety attitudes, increased team communication and the ability to truly apply these safety skills 24/7. The benefits of the SafeStart home program include improved safety performance at work and off-the-job in ways that can’t be achieved with other programs.
Most people care more about the safety of their loved ones than their own, so having a program that can be taken home has great advantages. Such programs demonstrate the employer’s commitment to the safety of employees and their families, which contributes to a thriving positive safety culture. But they also lead to fewer off-the-job injuries, better workplace productivity and improved retention of safety training achieved through teaching others.
Understanding the value of this, High Liner has implemented a number of initiatives (including contests, events and rewards) for both the employees and their families as part of the SafeStart program.
Personal Accountability
Once High Liner shifted their view of safety from a mandated process to a collaborative one, they started noticing results. Empowering employees to be involved in the process has not only filled in the safety gaps but also provided an incentive for them to take personal accountability—for themselves, their co-workers and their families. Additionally, the peer-to-peer reinforcement of safety has made the violation of safety rules a rare occurrence. Lamontagne added,
Now that we’ve integrated SafeStart into our culture, the amount of interaction between employees and management concerning safety has increased significantly. We rarely see any incidents involving lack of PPE, which speaks to personal accountability on the part of the employees.
Driving Safety
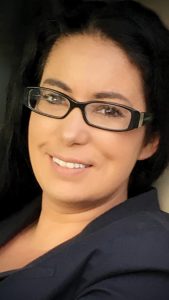
High Liner’s third key area of safety to address was driving (which applies to on-the-job and off-the job safety). One of the biggest causes of automotive fatalities is distracted driving; when drivers allow their minds—or eyes—to wander long enough to lead to an accident.
Complacency, one of the four states identified in SafeStart, causes drivers to feel they can safely take their eyes and mind off the road because after driving for a while, it’s easy to get comfortable and forget just how dangerous it can be.
Compounding the problem are other states of mind like rushing, frustration and fatigue. These can further contribute to taking eyes and mind off the task of driving and influence in-themoment decisions that increase the risk of collision. Lamontagne comments, “Since becoming involved in SafeStart, my driving behavior has improved significantly because the truth behind the state-to-error risk pattern really hit home.”
With SafeStart, High Liner found a catch they won’t release. With the remarkable improvements they’ve seen in their already good safety program, they can comfortably live by the phrase “zero accidents is possible.” Through safety culture, management involvement, common language and peer-to-peer reinforcement, High Liner employees work together to ensure everyone’s safety—their own, their colleagues’ and their families’—24/7.
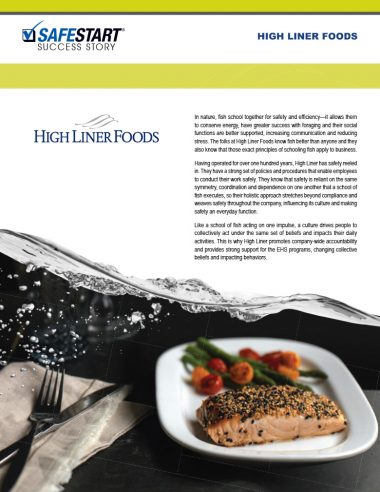
Get the PDF
You can view or download a PDF of this case study using the button below.