Georgia-Pacific is one of the world’s leading manufacturers of tissue, pulp, paper, packaging, building products and related chemicals. The company employs 40,000 people and has approximately 300 manufacturing facilities across North America, South America and Europe, ranging from large pulp, paper and tissue operations to gypsum plants, box plants and building products complexes.
Safety and Health Vision
The Georgia-Pacific vision for safety and health is to create long-term value by striving for safety and health excellence while achieving an injury-free workplace. To achieve that vision, employees and teams throughout the company focus on communicating that vision, identifying risks, developing prevention programs and tools, training and equipping employees, and monitoring and measuring both leading and lagging indicators to better understand progress towards an injury-free workplace.
Facilities are encouraged to use a number of resources and programs to achieve this vision. Some choose the U.S. Department of Labor’s Occupational Safety and Health Administration (OSHA) Voluntary Protection Program (VPP). To participate in the OSHA VPP program, facilities undergo a rigorous evaluation process to demonstrate how their policies and programs maintain excellent health and safety conditions for all employees. Georgia-Pacific has 81 sites recognized by the OSHA VPP program.
Some GP facility teams use the SafeStart program as one tool to achieve their safety vision. The members of the Central Safety Committee for the Halsey, Oregon site answered our questions to share the highlights of their SafeStart experience with others. The Halsey site produces consumer products including Quilted Northern® tissue and private label consumer products.
The Requirement
The Central Safety Committee was seeking something beyond simple injury reduction; they wanted to further demonstrate to employees that safety is a VALUE—not a program or effort—at Georgia-Pacific. Results had plateaued for over 3 years. It was felt that a change was needed.
After employees attended a SafeStart presentation at the Western Pulp and Paper Conference in December 2007, SafeStart was proposed as the required change.
While Georgia-Pacific had a number of comprehensive programs to advance their safety efforts, the Halsey mill saw SafeStart as a creative program to help re-energize their safety initiatives and improve results. The success in engaging employees at the Halsey mill then led the company to recognize the potential of SafeStart, so other facilities were encouraged to assess the program as a tool to use.
One manager remarked, “We were all looking for something new and unique which could be of value to our mill.”
A group of salaried and hourly employees from Halsey was sent to Dallas for a public SafeStart trainer certification in March 2008. The same manager commented on some of the critical factors contributing to their decision: “We saw that SafeStart was easy to understand, it promoted personal safe behavior and personal accountability for safety.”
After returning to Halsey, the group made a presentation to the Central Safety Committee and everyone was in alignment to move ahead with training the workforce.
The Implementation
The Halsey mill devised a work schedule with “reliefs” to keep equipment running while training of all the employees was completed. Volunteers were requested to work overtime to run the equipment on their day off (versus mandatory overtime for training after shift). This worked very well and prompted excellent participation.
Hourly employees were chosen to be the trainers for the hourly workforce. This method was adopted to suit the culture, to promote buy-in and greater employee ownership of the SafeStart program. Ten to fifteen people were trained per class over the course of six weeks. The Mill Leadership Team supported the SafeStart process from the beginning and later embraced it after receiving training themselves.
Employee Extended Application Unit classes have begun and will continue to be a critical component for sustainability of SafeStart and incident prevention
An innovative “relief system” greatly reduced overtime needs and facilitated the integration of the SafeStart program for both management and employees.
Communicating a Culture of Responsibility
SafeStart has become a part of the common language at the Halsey mill: the mill manager’s weekly safety memo, articles in their weekly and monthly newsletters by the mill nurse and other management contributors and signage in key parts of the mill all utilize SafeStart terminology.
SafeStart concepts are being incorporated into the Halsey mill’s JHAs, SOPs, Incident Analysis, Safe Work Permits, and most mill-wide communications from the safety department and key leaders.
Employees are also using the SafeStart language on the work floor and in many of their activities: “We definitely have seen an increase in the amount of employee involvement and volunteering in safety activities. Also, you hear SafeStart stories being told in the breakrooms with employees sharing how SafeStart has helped them prevent injury at home.” The impact of positive communication at the Halsey mill is clear; “Safety is a value for each individual. We have seen positive culture change with SafeStart,” remarked one of the facility’s managers.
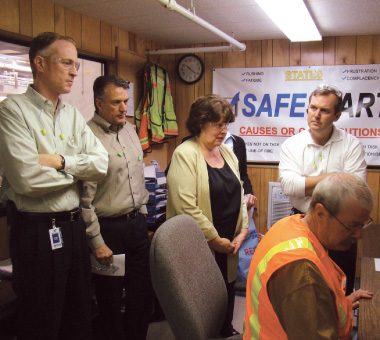
When an injury occurs now, people want to know details and discuss it. In the past, injuries were just accepted and expected. People are looking out for each other when they recognize their co-workers are in a state which could lead to a critical error and an injury. An employee with 35+ years of service said that SafeStart is the best training he has ever seen at this mill. The Halsey mill has dozens of employees who have talked about how they have used Critical Error Reduction Techniques, both at work and, especially, at home, to prevent incidents and/or injuries.
SafeStart provides each person with a ‘skillset’ to prevent accidents. It is an on-going process that you can learn from each day. We are very satisfied with SafeStart and what it has done and continues to do for our mill and employees while at work and at home. SafeStart is a self-triggering process and creates greater awareness. This selfawareness also helps people better see when others are at risk
– Manager
The Results of Innovation and Integration
A commitment to change and improvement has continued to guide decisions at the Halsey mill. In order to demonstrate safety as a value, in the last two years, Halsey has been concentrating on leading rather than lagging indicators: near misses versus recordables. They achieved a 75% reduction in injuries from 2008 to 2010 and their severity rate was also significantly reduced during the same period. Full investigations and action plans regarding serious near misses are of current concern. Reducing hazards and risks is the primary focus, with the intention of making incidents as preventable as possible.
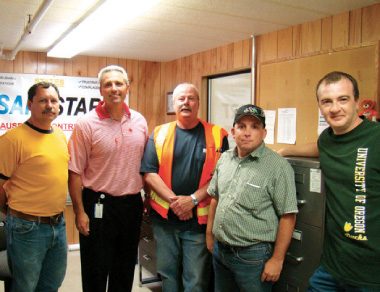
Reliability is also an effort for overall safety. More reliable equipment reduces risks and guards against such leading states as rushing and frustration as contributors to incidents. Being much more proactive rather than reactive is the essence of their approach.
The contribution of safety to quality and productivity has also been recognized.
“While we cannot directly quantify productivity and quality improvements in relation to one source (indeed, there are a number of factors that contribute to these improvements), there is no question that we have seen a dramatic improvement in our safety culture, our leading indicators, and our lagging indicators such as the OIR and DART rates. We believe that safety is indeed a value proposition and a safe workforce is critical to obtaining productivity and quality gains.”
— Manager
The cumulative result of efforts at the Halsey mill was a 58% injury reduction in one year through numerous safety improvements, including SafeStart.
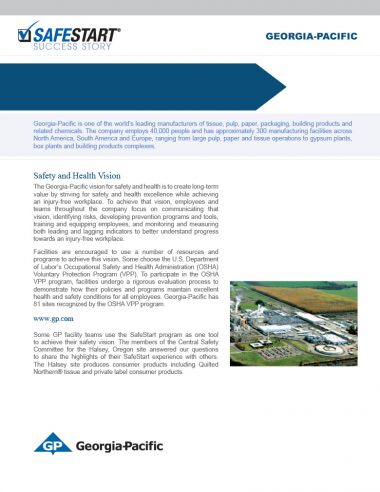
Get the PDF
You can view or download a PDF of this case study using the button below.