This article by Ray Prest was orginally published in the
Winter/Spring 2019 issue of the Safety Decisions Magazine
It’s amazing to watch the safety industry collectively reexamine how we measure safety performance. Gone are the days when safety managers plug incident tallies into a spreadsheet and then try to manage things so the next tally will hopefully be lower. Companies are becoming increasingly sophisticated in tracking a wide range of safety events.
The search for leading indicators is slowly but surely leading the industry to look for more predictive data, including near misses, performance data, and other site-specific information that may be indicative of future incidents. Behind this flurry of activity is a line of thinking that goes something like this: if we can find signs that a workplace incident is more likely to happen, we can take steps to prevent it from happening.
Ideally, we can find indicators to anticipate future safety outcomes. But in order for us to predict outcomes, we need to understand the process that produces them. And this is where well-meaning EHS folks can get tripped up.
Safety is a process and injuries (and other incidents) are the outcome of that process. It’s extremely difficult to measure the safety process. And it’s relatively easy to keep track of outcomes, especially when they are discrete events like injuries. As a result, people have a natural tendency to focus on outcomes rather than on processes—even though they know that processes are more important for the long-term health of a workplace.
We often think of safety processes and outcomes as inseparable. And in most cases, they’re closely related. An inadequate safety system will likely lead to numerous injuries. Conversely, a strong safety process will probably excel at preventing workplace incidents.
But even though process and outcome are tied together, they’re not the same thing. An employee can go years without suffering a single injury, even though he or she never wears personal protective equipment (PPE). I think we can all agree that this is a positive outcome despite an incredibly bad process. At the same time, a worker can take reasonable steps to avoid an injury and still end up in the hospital thanks to an unanticipatable incident. A proactive process is no guarantee.
Outcomes tell you what happened in the past. If you look at the injury rates for your workplace, I can tell you how many lost-time incidents occurred in the past 12 months. But I can’t tell you how many workers will get hurt tomorrow, let alone what your Total Recordable Incidents (TRI) will be next year.
Processes tell you what is likely to happen in the future. I may not be able to predict with 100% accuracy what your exact incident rate will be next year, but if I know what your safety process is, I will have a decent idea of the range of likely outcomes.
The search for leading indicators is like Moneyball for safety. The goal is to discover the underlying forces driving success or failure. We want to sift through the luck, circumstance, and other statistical noise in order to better evaluate the true safety performance of our people and systems.
The only problem is that no one’s quite sure what those leading indicators look like. All too often, in the rush to discover leading indicators, safety professionals don’t realize that they’re actually capturing new lagging indicators.
In many cases, it’s not even clear whether something is a leading or lagging indicator. Take near misses, for example. A strong case can be made that a near-miss report is an outcome because it documents something that happened. But many safety professionals are able to use near-miss data to identify potential issues and take corrective action before anyone is seriously hurt.
If you’re confused about what leading indicators look like or how to go about finding them in your workplace, you’re not alone. No one else quite knows either. But as it stands, we’re already taking a giant step as an industry by admitting that our current safety data isn’t sufficient—that what we know right now isn’t enough and that we need to do better. And now we need to do the work required to figure out exactly what useful leading indicators look like.
The Campbell Institute recently issued a guide to leading indicators that suggests “an organization should not spend too much time nailing down the ‘perfect’ leading indicator, mainly because a universal perfect indicator does not exist, and also because it is impossible to know the value of an indicator until an organization gives it a chance.” It’s important to admit that none of us is going to get it right away. It’s going to require a lot of trial and error.
We need to share our successes and failures and focus on developing best practices and a broader framework of understanding. If we do, we may start to notice site-specific solutions and patchwork approaches transforming into rigorous indicators that are collected effectively and put to proper use.
The good news is that the work you’ll do iterating indicators is not wasted. Even something that turns out to be a less-effective indicator is far better than waiting on outcomes. Quantity of predictors is important. So, too, are quality ones, and you’ll discover those throughout the process by comparison and measuring progress.
Personally, I think there’s a lot to be gained from measuring learning and knowledge retention. If we can track how well safety training works and how much employees remember, we can make changes to the education process that will lead to real improvements downstream on the shop floor where injuries happen or, hopefully, don’t.
You could also look to how employees behave outside of work. People trading in their flipflops for steel-toe boots while cutting their lawn, using a proper step stool instead of a kitchen chair to change a lightbulb, or putting the cell phone out of reach while driving—these are the ultimate indicators that your training and corporate safety mind-set have truly sunk in.
What people do habitually on their own without anyone watching will strongly correlate with what they do at work. If they wear PPE at home, they’ll likely wear it at work. And if you can’t get workers to follow safety guidelines when they’re off the job, that’s a strong sign there’s still work to do.
Capturing indicators of off-the-job, self-directed safety behaviors is obviously difficult for organizations to do. It’s also tough to gauge how much people actually learn from training sessions. But both are examples of how wide-open the search for leading indicators is. Anything is fair game if it’s indicative of how people think about safety. Now, it’s up to you to get creative and determine how safe your people actually are.
Ray Prest is the Director of Marketing at SafeStart, a safety company focused on human factors solutions that reduce preventable death and injuries on and off the job. A columnist for Safety Decisions since 2015, Ray’s been helping people learn about safety and training for over 20 years. Read more at safestart.com/ray.
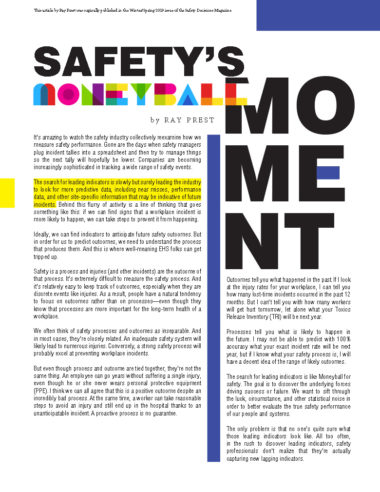
Get the PDF version
You can download a printable PDF of the article using the button below.