This article by Gary A. Higbee, EMBA, CSP was originally published in the May 2003 issue of Industrial Safety & Hygiene News.
Work on these nine steps and watch your frustration over safety’s lack of support decrease as the safety performance of your organization improves.
The safety culture will begin to change and most people will not even know their attitude about safety is changing.
1. Walk the talk 100 percent of the time.
At home, work or play we cannot stray or the message is lost. Be proud of what you do and dedicated to the safety task.
2. Meet the minimal safety standards of OSHA, MSHA, etc.
Standards are just a beginning and certainly do not guarantee an injury-free workplace. But they are specific requirements—and that makes them very hard to ignore. Safety issues may not be visible to the untrained or unwilling eye, but standards are easy to read and visible to everyone.
3. Find supporters & enlist their help.
Find like-minded people who understand the concepts of compliance, conditions, risk, reward and behavior. They’re somewhere in every organization.
4. Promote the corporate policy on safety.
Copies should be posted everywhere possible. The statement sets the position of upper management on workplace safety. We all know local management may have a completely different view of safety given the pressure on them for production, quality and profitability. You’ll need this statement to reinforce the culture change.
5. Train your supervisors.
It’s surprising how little supervisors know about their responsibilities for workplace safety. They understand very well their responsibilities for production, quality and cost. These responsibilities are very visible and they have grown up with them. Safety is not that visible and supervisors need training on these issues.
6. Provide meaningful data to managers.
Managers receive reports every day on productivity, quality and cost—so why do we often only report safety data on a monthly basis? Develop reports that are easy to read, standardized, accurate and easy to forward or pass on. Report daily on regulatory contacts, critical safety concerns, injuries, property damage and near misses. Monthly you should report on your rates, measurements toward project completion and activities like training, inspections or audits.
7. Hold managers & supervisors accountable.
These responsibilities cover things they can control, such as their employees’ attendance at training sessions, timely and accurate accident investigations, required audits, etc.
8. Recognize safety achievements.
Give everyone credit that you possibly can. Thank them for their efforts, or you may not get the same effort the next time.
9. Gain access to top management.
By providing the information managers need and keeping them informed, you’ll naturally create lines of communication. Capitalize on your opportunities to communicate with upper management—do not avoid them.
Gary is an expert in safety management systems and organizational change, he is a two-time past president of the Hawkeye Chapter of the ASSP and past Regional Safety Professional of the Year. In 2010, Gary was awarded the Distinguished Service to Safety Award, the top individual safety award from the NSC.
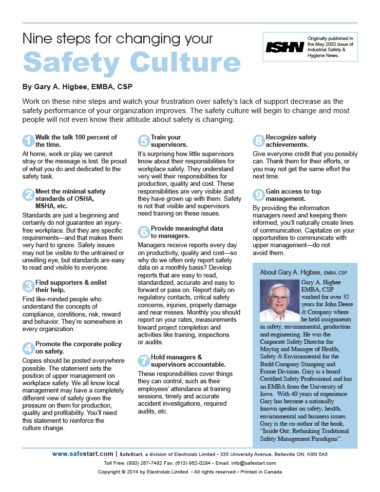
Get the PDF version
You can download a printable PDF of the article using the button below.