Simmons
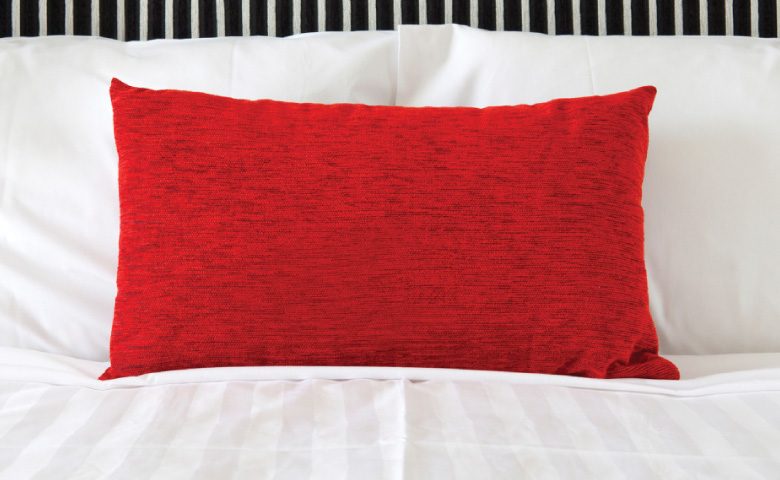
Comment la compagnie Simmons a transformé la sécurité en profits concrets
Vue d’ensemble
L’entente implicite des milieux de travail veut que la formation reliée à la sécurité et le respect des règlements en santé et sécurité au travail, soient des dépenses qui ne se traduisent pas en éléments positifs concrets. Les usines et les industries mettent en pratique des mesures de sécurité afin de répondre aux exigences de normalisation, afin de réduire les coûts d’assurance contre les accidents du travail et afin d’éviter des frais de litige élevés. Dans le cadre d’une perspective financière, les initiatives reliées à la sécurité au travail représentent fondamentalement des coûts d’opération et non pas des efforts qui favorisent une productivité accrue, des réductions substantielles des coûts d’opération et des profits à la hausse. Toutefois, la compagnie Simmons, l’un des plus grands fabricants mondiaux de matelas, a récemment réfuté cette notion et ce, de manière fulgurante!
« Nous n’avons pas seulement fait de la sécurité un programme autosuffisant » explique le docteur Jonathan Dawe, directeur du service des ressources humaines secteur de la sécurité, du mieux-être et d’indemnisation des travailleurs chez Simmons. « La sécurité est devenue partie intégrante contribuant nettement à notre succès. »
En effet, non seulement les accidents de travail chez Simmons de même que les coûts liés aux réclamations des employés ont été réduits de plus de 75 %, la productivité et les revenus ont augmenté substantiellement. Et, malgré la récession récente et le rétablissement anémique – qui ont posé des problèmes sérieux pour de nombreux fabricants américains – Simmons a prospéré et s’est développé toujours plus. Docteur Dawe décrit l’ascension de Simmons tout comme l’histoire de Cendrillon – et ce, sans exagération de sa part!!
Antécédents
Tout comme de nombreuses autres industries impliquant du travail à la chaîne, la compagnie Simmons rémunérait ses employés sur un système basé à la pièce. Le plus de pièces produites par l’employé, plus la rémunération était élevée. La prémisse de base de ce principe économique était le suivant : une productivité accrue. Malheureusement, l’une des conséquences néfastes de cette approche s’avère la sécurité au travail. Pour réussir à accomplir davantage, les employés prennent parfois des « raccourcis » ou modifient la mécanique de la machinerie. Les employés qui ne sont pas parfaitement attentifs à leur travail sont éventuellement victimes d’accidents.
Comme dans presque tous les types de fabrication, le montage de matelas implique l’utilisation d’appareils de machinerie lourde; lorsque certains de ces appareils ne sont pas utilisés correctement, ceux-ci peuvent s’avérer très dangereux. Des appareils conçus pour l’enroulement, transforment des fils métalliques en ressorts pour matelas, ces derniers étroitement serrés. Les ouvriers manient des cloueuses à poussoir et gâchette pour assembler les bâtis et utilisent des agrafeuses pour y fixer le rembourrage. De gigantesques machines pour le ouatinage réunissent les panneaux pendant que des lignes de travailleurs peinent aux machines à coudre industrielles. Objets de toutes sortes, bruits nombreux, immenses appareils de travail et poussière, tous ces éléments contribuent à créer des dangers potentiels.
Le docteur Dawe est à l’emploi de la compagnie Simmons à la suite d’un contrat d’une durée de deux années, chez BellSouth, et ce, à titre de responsable de la sécurité et de la formation. Dès le début de son travail chez Simmons, le docteur Dawe reconnut l’immense défi à relever : il faut faire bien plus que respecter les règlements en ce qui concerne la santé et la sécurité du travail, bien plus que tenter d’enrayer les risques et dangers en milieu de travail. Simmons avait besoin d’élaborer une vision et des buts bien précis pour tout ce qui touchait à la sécurité au travail. Le docteur Dawe élabora un plan en deux volets : le premier, mettre en place un manuel de sécurité – (ce que la compagnie n’avait pas) et dans un deuxième temps, préparer des ateliers de formation pour les superviseurs, les directeurs des divers secteurs d’opérations et les gestionnaires de l’entreprise.
Peu de temps après l’arrivée du docteur Dawe chez Simmons, une nouvelle équipe de gestionnaires, dirigée par le président directeur général, monsieur Charlie Eitel, devint les dirigeants de la compagnie. Lorsque le docteur Dawe approcha cette nouvelle équipe, afin de mettre en place des mesures de sécurité, il n’eut à convaincre personne. « Charlie Eitel, le président de la compagnie, Bob Hellyer, président du service des finances, la vice-présidente du service des ressources humaines, Rhonda Rousch, tous étaient persuadés de la nécessité de la mise en place d’un programme de sécurité au sein de l’entreprise», raconte le docteur Dawe. Les superviseurs étaient conscients des défis à relever, ont donc débloqué des budgets pour la sécurité et ont guidé l’application des changements au sein de la compagnie.
Oeuvrant de près avec l’équipe de gestionnaires, le docteur Dawe mit en place un audit des conditions de sécurité et ce, aux 18 sites Simmons. Cet audit était réparti en une semaine d’inspection « contrefaite » à la façon des inspections réalisées par les représentants du Ministère du travail. Un groupe de vérificateurs examinèrent attentivement les dossiers en filières, les ateliers de fabrication et le matériel de formation disponible. Un nombre de membres furent également interviewés.
Ces auditeurs découvrirent, entre autres, que plusieurs membres ne portaient pas l’équipement de protection individuel tel les lunettes protectrices, de protection pour les mains ou les chaussures à embout protecteur. Plusieurs travailleurs affectés aux ateliers de fabrication portaient des vêtements amples qui pouvaient se coincer dans les appareils.
Les résultats de cette vérification révélaient que Simmons devait corriger les dangers internes; que la compagnie se devait aussi de mettre en place de la formation concernant la sécurité de même que des procédures à cet effet. La réponse se traduisit par des efforts concrets chez tous ses membres. La compagnie établit donc un programme détaillé, concernant la sécurité, réparti en quatorze (14) points, ces derniers définissant les objectifs visés en sécurité et les stratégies correspondantes. Les équipes de direction de chacun des sites Simmons développèrent des plans d’actions spécifiques à leur lieu de travail. Ayant déjà un groupe de superviseurs convaincus, il était vital de recruter aussi les ouvriers des lignes de montage à cet effort communautaire. Simmons mit donc en place des comités responsables de la sécurité, ces comités étant largement composés des employés. Ces mêmes comités se rendaient responsables des inspections de la sécurité, de la formation, des enquêtes d’accidents et de l’enraiement des dangers. Dès que la réunion de ces efforts devint concrète, Simmons débuta des séances de formation.
En effet, non seulement les accidents de travail chez Simmons de même que les coûts liés aux réclamations des employés ont été réduits de plus de 75 %, la productivité et les revenus ont augmenté substantiellement.
La formation
Le docteur Dawe savait fort bien qu’un programme de sécurité efficace doit se préoccuper d’abord et avant tout des questions reliées aux conditions dangereuses, à l’ergonomie, une gestion selon la conformité des règlements et enfin, à une formation en sécurité conforme aux règlements. Cependant, le docteur Dawe réalisait également que ces seules initiatives ne permettraient qu’un succès partiel. Il fallait aussi l’établissement d’un programme de sécurité détaillé, ce dernier maximalisant l’engagement des employés et minimisant les erreurs « humaines » contribuant à des accidents de travail.
La sécurité axée sur le comportement offrait une solution intéressante. Malgré tout, le docteur Dawe croyait fermement que Simmons avait besoin d’un élément « déclencheur » plus expéditif, relié aux efforts de l’entreprise dans la mise en place de son programme de sécurité.
Le docteur Dawe avait aussi des réserves quant à la « bureaucratie », la lourdeur des procédures administratives de même que de toutes les exigences liées à l’observation des comportements, tel que l’exigence typique des programmes de sécurité axée sur le comportement.
Au cours de ses recherches, le docteur Dawe découvrit une copie préliminaire du programme SafeStart. Il réalisa immédiatement que celui-ci représentait le complément parfait aux éléments principaux du programme de sécurité, élaboré chez Simmons. Selon le docteur Dawe, son choix était légitimé par de nombreuses raisons.
« Tout d’abord, ce sont des connaissances liées au bon jugement » dit-il. Le matériel est présenté de façon telle, que tous nos employés puissent s’y identifier facilement, que ce soit dans le cadre du travail, à la maison, en participant à des activités sportives ou toute autre occupation. L’élément le plus attrayant du programme SafeStart était, selon le docteur Dawe, la vulgarisation du contenu.
Tout en étant basé sur plusieurs principes similaires de la sécurité axée sur les comportements, celui de SafeStart offre une approche plus simple et plus directe, afin de sensibiliser les participants et de susciter des changements de comportements. Le programme SafeStart s’appuie sur quatre (4) erreurs critiques, celles-ci provoquant entre 80 % et 90 % de tous les accidents en milieu de travail. Ces erreurs sont : l’inattention du regard; la distraction; se déplacer vers ou être dans « la ligne de tir »; et la perte d’équilibre, d’adhérence et de prise. Le programme SafeStart se concentre ensuite sur les facteurs humains ou « états » de chacun qui, typiquement, contribuent ou encore sont la cause d’une erreur critique. Ces « états » comprennent la précipitation, la fatigue, la frustration et l’excès de confiance.
Les employés de chez Simmons étaient fin prêt à mettre en pratique le programme SafeStart. Peu de temps après, Simmons faisait le lancement de l’implantation du programme SafeStart, et ce, pour ses dix-huit (18) sites. Tous les employés et tous les gestionnaires de chacun des sites Simmons participent à la formation SafeStart. Chaque personne participe à cette formation répartie de la manière suivante : cinq sessions, d’une durée de deux heures et demie chacune, dans le cadre d’une classe composée de 15 à 20 élèves.
Tous les cours sont dirigés par des animateurs qualifiés et des vidéos sont également visionnées. Ces cours enseignent aux employés, aux directeurs des secteurs d’opérations, de même qu’aux gestionnaires, comment reconnaître les états précités, soit la précipitation, la fatigue, la frustration et l’excès de confiance, qui mènent parfois à des erreurs critiques. Néanmoins, ce qui a particulièrement plu au docteur Dawe, c’est que le programme SafeStart permet aux participants de « réagir » aux états, de manière à éviter de commettre des erreurs critiques, celles-ci provoquant bien souvent des accidents. De plus, les effets du programme se répercutent bien plus loin qu’en milieu de travail seulement; les participants réalisent que les enseignements du programme SafeStart s’appliquent tout aussi bien pendant leur conduite automobile, leur participation à des activités sportives, ou bien lorsqu’ils exécutent des travaux autour de leur résidence.
Dans des buts de renforcements positifs, Simmons a également affiché de grandes bannières à chacun de ses sites, celles-ci mettant l’accent sur les quatre états, soit la précipitation, la fatigue, la frustration et l’excès de confiance. Simmons a également inclus dans son formulaire de rapport d’enquête d’un accident, les concepts du programme SafeStart. Les représentants de la compagnie utilisent également le langage pertinent du programme de formation de SafeStart, lors de réunions et dans la rédaction de ses notes de service.
Simmons a formé les employés affectés à la production, de chacun de ses sites à surveiller et à faciliter l’intégration du programme SafeStart.
Ces facilitateurs ont la responsabilité d’organiser et de présenter la formation SafeStart, obtenir la rétroaction de même que faire l’évaluation du succès de la mise en place du programme. « Lorsque les employés sont les premiers responsables de tout le processus, il n’est plus question d’une situation où « les gestionnaires nous disent quoi faire », ajoute le docteur Dawe. « Ce sont les pairs qui se guident l’un l’autre, qui prennent soin l’un de l’autre. Cette situation accroît de manière significative l’engagement des employés vis-à-vis la sécurité et le succès de l’implantation du programme.
De surcroît, pour tous les employés affectés aux ateliers, Simmons accorde des récompenses aux personnes atteignant des succès d’excellence. La compagnie a aussi ajouté au programme, le principe du boni appelé « Gaspillage-Zéro ». Le gaspillage étant, selon la définition de Simmons, n’importe quel élément n’apportant aucune valeur additionnelle aux produits finis ou aucun bénéfice supplémentaire aux consommateurs.
« Les accidents sont un gaspillage, de l’équipement détruit est un gaspillage, le temps utilisé à mauvais escient est un gaspillage, les primes d’indemnisation des travailleurs sont un gaspillage » précise le docteur Dawe. « Une sécurité déficiente est un souci financier pour une entreprise. Le principe du « gaspillage-zéro », premier élément de la émunération des employés, rappelle le principe du « partage des dividendes ». Plus une entreprise se départit du gaspillage, plus les revenus sont élevés, plus les rémunérations le deviennent aussi ».
L’entreprise Simmons relie ce boni à quatre secteurs élémentaires de son programme : la sécurité, la qualité, le service et l’économie des coûts. S’inspirant de l’importance accordée à la sécurité par Simmons, la compagnie a fait de la sécurité la portion la plus importante du boni.
Il reconnut l’immense défi à relever : il faut faire bien plus que respecter les règlements en ce qui concerne la santé et la sécurité du travail, bien plus que tenter d’enrayer les risques et dangers en milieu de travail. Simmons avait besoin d’élaborer une vision et des buts bien précis pour tout ce qui touchait à la sécurité au travail.
Les résultats
Les résultats obtenus par la compagnie Simmons sont tout simplement extraordinaires. Le taux d’incidents déclarés a connu une baisse, passant d’un pourcentage de 17,6 % de blessures enregistrées et/ou de maladies professionnelles, sur un total de 100 employés à temps plein au cours de la première année, à 4,5 % au cours de la troisième année (voir l’annexe 1). De plus, l’augmentation de la productivité est devenue directement proportionnelle à la mise en place d’une sécurité accrue. L’entreprise Simmons a enregistré une productivité accrue de plus de 12 % entre la première année et la quatrième année, atteignant ainsi le niveau le plus élevé de toute son histoire.
Les sites des usines Simmons, autrefois considérés presque « impossibles à assurer » par les compagnies d’assurances responsables d’indemnisation des travailleurs, sont maintenant reconnus, par ces mêmes compagnies, comme les meilleurs parmi leurs pairs. L’atteinte de ce nouveau sommet de sécurité a également eu d’énormes impacts en termes de primes. De fait, les coûts reliés aux réclamations des employés se sont littéralement effrités, chutant de 2,5 millions $ en la première année à près de 609 637 $ en la troisième année, des épargnes plus que révélatrices (voir annexe 2).
L’une des usines de Phoenix a performé de façon tellement éloquente, en termes de sécurité, qu’elle fait maintenant partie du programme de protection volontaire de OSHA. La participation à ce programme permet à l’usine de Phoenix d’être exempte des inspections de OSHA, pour une période de trois (3) ans. Cette usine est la première, dans le domaine de la fabrication de matelas, à être reconnue de façon aussi probante.
Une diminution des coûts d’opération, une productivité accrue et une sécurité améliorée jumelées à des changements en profondeur de la culture organisationnelle, ont permis à Simmons de prospérer. Les ventes et les salaires ont augmenté de manière ponctuelle au cours des trois (3) dernières années (voir annexe 3) et la compagnie Simmons a complété, tout dernièrement, la construction de deux (2) nouvelles usines aux États- Unis. (En considérant le rôle vital joué par SafeStart au sein de la compagnie, Simmons exige maintenant que tous les employés embauchés pour les nouveaux sites complètent avec succès la formation du programme SafeStart et ce, avant même que les sites ne soient fonctionnels)
En définitive, cependant, la sécurité s’avère beaucoup plus que des statistiques. Selon le docteur Dawe, le programme SafeStart donne à chacune et à chacun, une occasion ou un élément à utiliser, afin de s’aider eux-mêmes ou d’aider les autres employés de la compagnie.
« L’élément motivateur du programme SafeStart réside principalement dans le fait qu’une personne peut décider de faire quelque chose » dit-il. Les gens n’ont pas besoin d’attendre une décision administrative; ils n’ont pas de permission à demander. On leur remet un processus, une permission et de la protection, et ce, tout de go. »
De toute évidence, ce principe semble fonctionner, puisque la compagnie Simmons a récemment été citée au magazine « Fortune », selon lequel Simmons fait partie des cent meilleures compagnies pour lesquelles quelqu’un pourrait souhaiter travailler; un véritable témoignage de succès à la qualité du milieu de travail sécuritaire que Simmons a réussi à créer.
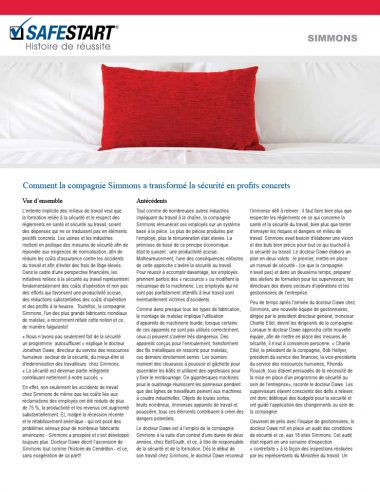
Obtenir la version PDF
Vous pouvez consulter ou télécharger l’étude de cas en PDF à l’aide du bouton ci-dessous.